KEYFLEX MEMBRANE KEYPADS
KEYFLEX Membrane Keypads & Decals
The Keyflex Company Pty Ltd has led the way in membrane switch production since 1993, with its headquarters in Australia. At Keyflex, we pride ourselves on our expertise in the design and engineering of membrane keypads and the mass production and manufacturing at scale. We supply our membrane keypads globally, to all corners of the world. Our skilled team first comprehends our clients' requirements to ensure every keypad is easy to use, durable, and long-lasting. We select materials that are bendable, conduct electricity efficiently, and can withstand changes in temperature and humidity. We prioritise comfort and aesthetics, making sure our products are both practical and visually appealing. With advanced printing techniques, we create custom decals that seamlessly match our keypads, blending function and style. Dedicated to sustainability, we employ energy-efficient methods and use recyclable materials whenever feasible. We collaborate closely with clients to craft solutions that meet today's needs and foresee future demands. This approach guarantees Keyflex membrane keypads are reliable, enhancing user engagement with technology for smooth, enjoyable experiences. Our commitment to innovation allows us to consistently provide exceptional components for diverse industries, from Australian markets to global sectors.
No drawing? No problem! We only need some basic design information filled out on our membrane switch and decal quotation forms to quote.
LGF (Light guide film) Keypads with integral LED backlighting
The light guide film (LGF) introduces built-in LED backlighting to Keyflex membrane keypads and front panel decals, enabling text and entire key illumination. Our LGF ensures uniform light distribution across the keypad or decal front panel while maintaining a thickness comparable to standard membrane switch panels. Integrating LED backlighting requires thoughtful consideration and meticulous planning to achieve successful implementation in a design. There are crucial design criteria and limitations to understand, so if an integrated backlight is a feature you're considering for your design, we encourage you to contact Keyflex in West Leederville, Australia, directly for more detailed information. Our experience since 1993 ensures we can assist effectively.
Outstanding Reliability for membrane switches
Keyflex membrane keypads, materials and components are tested for operational lifespan to give you peace of mind
This short clip shows an actuation test where the life cycle of the keypad components with movement, such as a metal snap dome and overlay can be stress tested. A design can achieve 1M+ actuations.
Membrane Keypad Design - Materials
When considering the materials used in membrane keypad design, it's essential to choose those that can withstand varied environmental conditions while maintaining a high level of functionality. One popular material choice is the use of silver or carbon printed circuits on polyester (PET) films, known for providing a durable and flexible alternative to the traditional PCB approach. This method allows for intricate circuit patterns and is particularly advantageous in reducing the overall thickness of the keypad. Polyester films not only offer longevity and reliable performance across extensive temperature ranges but also resist moisture, making them suitable for both indoor and outdoor applications. By focusing on such reliable materials, Keyflex ensures that each keypad is both robust and responsive, perfectly aligning with our commitment to innovation in the field of human-machine interaction.
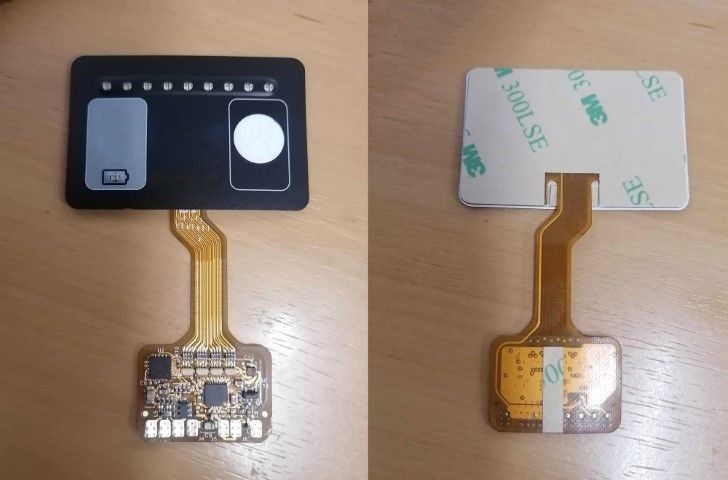
Flexible Printed Circuit (FPC or Kapton™)
Flexible Printed Circuit (FPC), often recognised by the brand name Kapton™, offers an essential level of flexibility and efficiency. This flexibility is crucial in creating advanced membrane keypads. These circuits are made from a flexible and durable polyimide film, which is well-known for its excellent thermal stability and ability to endure harsh environmental conditions. The flexible nature of FPCs allows for the development of complex, customised circuit designs that easily fit into various device structures. This provides a streamlined and efficient alternative to traditional circuit board arrangements. This flexibility not only helps in reducing the overall size of electronic parts but also ensures reliable performance in applications that need high flexibility and miniaturisation, like wearable technology and aerospace instrumentation.
Graphic Overlay materials
Graphic overlays for membrane switches are commonly made from polyester material. This choice of material is essential because it provides the necessary flexibility for seamless membrane switch operation, ensuring that the overlay does not fracture or break under pressure. In contrast, polycarbonate is often preferred as a base material for decals, overlays, and labels where movement is not a factor. However, when it comes to membrane switch applications, polycarbonate is not the ideal choice due to its limitations.
Polyester films offer various advantages for graphic overlays, including the ability to have a gloss or textured hardcoat finish directly embedded onto the film itself. This feature enhances the aesthetic appeal of the overlays while also adding a layer of protection. Additionally, it is possible to incorporate texturing and gloss finish areas using UV silk screening techniques applied to the base polyester.
When considering outdoor applications, it is crucial to prioritize UV stability to ensure longevity and durability. In this regard, Autotex XE stands out as a recommended option due to its excellent UV stability properties. By utilizing Autotex XE for outdoor graphic overlays, you can be confident that the overlays will resist the damaging effects of prolonged sun exposure, maintaining their vibrant appearance and functionality over time.
For medical applications, a specialized option known as Autotex AM is available. Autotex AM offers an additional layer of protection by incorporating an embedded antimicrobial agent within the surface coating of the overlay. This feature helps inhibit the growth and spread of harmful microorganisms, making it an ideal choice for medical environments where cleanliness and hygiene are of utmost importance.
In conclusion, the choice of materials for graphic overlays is crucial in ensuring optimal performance and longevity. Polyester films provide the necessary flexibility, while options such as Autotex XE and Autotex AM offer additional benefits such as UV stability and antimicrobial properties, respectively. By considering these technical details and selecting the most suitable material for specific applications, manufacturers can create high-quality graphic overlays that meet the diverse needs of their customers.
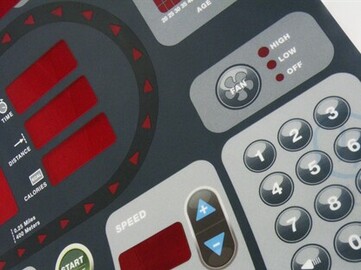
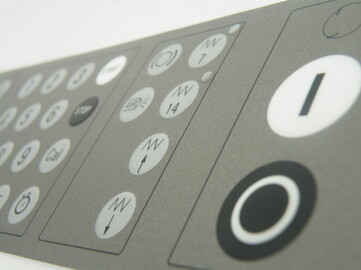